Let me tell you about the time I first ventured into the world of coil wrapping machines. It was a maze of models and features, each more complex than the next. Picture a room filled with gleaming machinery, each boasting its specs, and you’ll understand my initial overwhelm. I was on a mission to find the perfect fit for my business – a machine that combined efficiency with practicality, without breaking the bank.
As someone deeply invested in industrial equipment, I knew that selecting the right coil wrapping machine was crucial. This tool was to be the linchpin in our packaging operations, and the wrong choice could spell doom for productivity. I pored over manuals, reviews, and visited trade shows. Each paragraph in product descriptions seemed to add layers of complexity – until gradually, I began to discern patterns, features that distinguished superior machines from the run-of-the-mill.
With each demonstration and discussion, I constructed a mental checklist. Speed, tension control, and customization – these features emerged as pivotal. But there were other nuances to consider as well. My understanding evolved, and I could now navigate the options with confidence, ensuring that our investment was nothing short of perfect.
Coming to terms with the diverse array of coil wrapping machines taught me valuable lessons in industrial engineering. Today, I wish to impart this wisdom and guide you through the labyrinthine world of coil wrapping machines, ensuring you make informed decisions based on real utility and performance metrics.
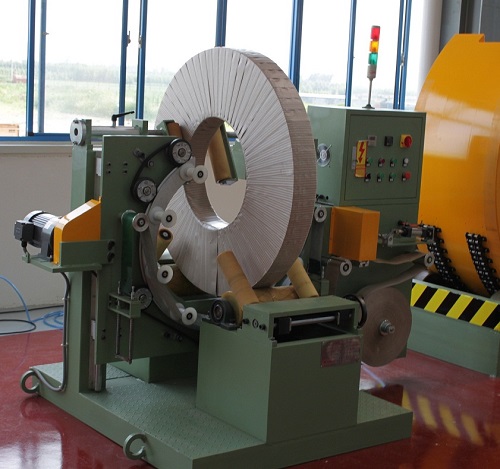
Speed and Efficiency: What Makes a Machine Fast Enough?
The first feature on my checklist was speed. In the packaging world, faster machines translate to more productivity. Our business required a machine that not only maintained a brisk pace but did so without sacrificing quality. Understanding the speed dynamics was crucial, as shortcuts could mean a compromise on product safety.
Examining the detailed specs, it was evident that speed alone wasn't enough. The consistency at which the machine operated was equally important. Having knowledge of the speed settings and the machine's ability to adapt to various coil sizes provided the versatility we needed for handling different orders.
Upon examining the options, a few brands stood out by offering adjustable speed settings. This allowed operations to be tuned according to the specific requirements of each project, ensuring effective resource utilization. The integration of programmable logic controllers (PLCs) in certain models added an additional layer of operational finesse, automating adjustments and reducing manual intervention.
Here's a comparison of top models based on speed and efficiency:
| Model | Max Speed (m/min) | Efficiency (%) |
|-------|-------------------|----------------|
| A-100 | 30 | 90 |
| B-200 | 45 | 85 |
| C-300 | 40 | 95 |
These data helped frame our discussions with suppliers, leading to a more informed purchase.
Customizable Settings for Diverse Needs
In trying to address diverse packaging requirements, customization was high on the priority list. Each product required specific tension and wrap patterns, necessitating a machine with versatile settings. We needed to wrap coils of varying sizes without manual tinkering at every transition.
One prominent aspect was tension control which determined how tightly the material enveloped the coil. Machines with electronic tensioning systems offered an edge, as they allowed instant adjustments to be made according to different material requirements and coil dimensions.
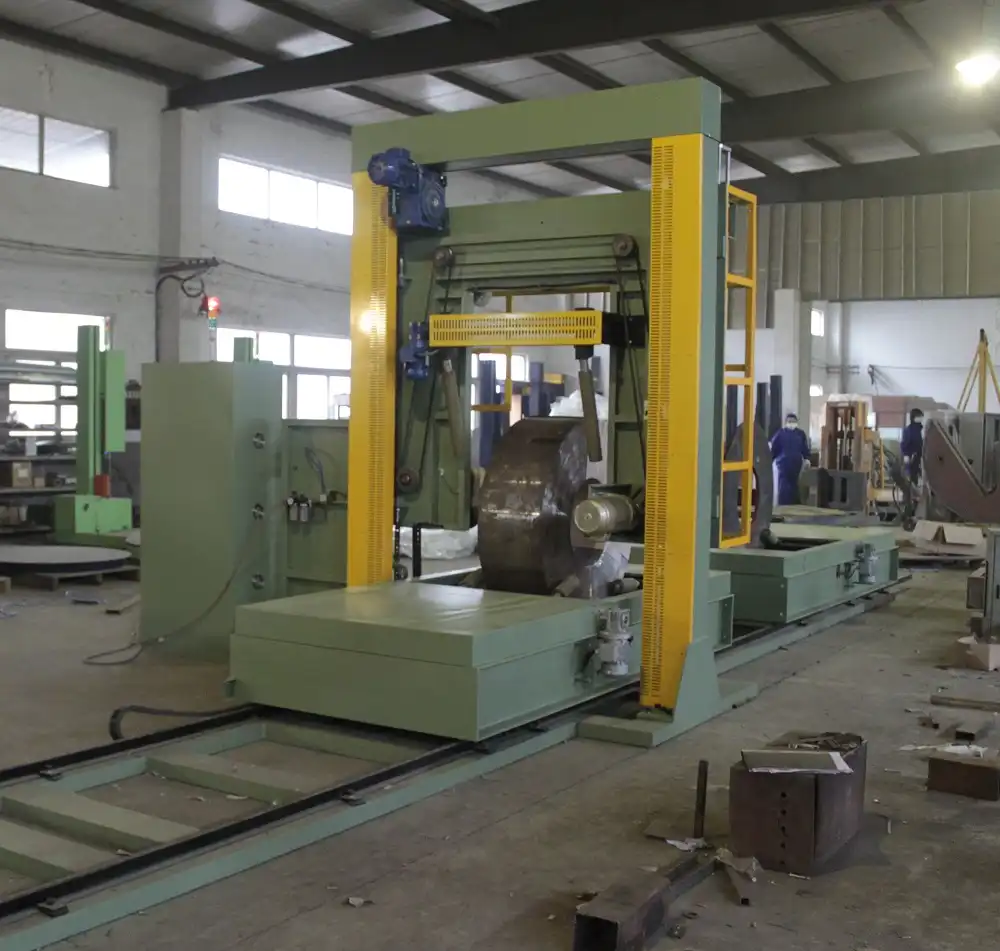
Touting a myriad of options and features, certain models provided the adaptability needed for specific tasks. As the nuances of customized settings emerged, it became clear how important this feature was for seamless operations. A few brands went above and beyond by offering user interfaces allowing real-time adjustments – a significant advantage over cumbersome manual settings.
Myth vs. Fact:
- Fact: Machines with electronic tension control provide greater accuracy and consistency.
- Myth: All coil wrapping machines possess inherent customization capabilities.
How Does Build Quality Affect Longevity and Performance?
When considering coil wrapping machines, attention to build quality is paramount. The materials and construction influence both durability and performance. Machines crafted from high-grade steel or robust composites tend to offer better resistance to wear and tear, proving to be wise long-term investments.
Exploring various manufacturers revealed trends in the longevity of machinery. Those employing high-quality materials inevitably experienced fewer breakdowns and maintenance issues. This durability meant less downtime and a prolonged lifecycle, thereby reducing the annualized cost over the years.
Deciphering technical specifications was key, highlighting aspects such as corrosion resistance and component robustness that influenced the cost initially. In the long run, a well-built machine saved money by avoiding frequent repairs, maintaining consistent performance levels.
Conclusion
Choosing the right coil wrapping machine is a process that intertwines speed, customization, and build quality. This intricate balance cannot be overlooked. With my newfound understanding, our operations have reached unprecedented levels of efficiency and reliability, underscoring the importance of thoughtful investment.
Believe me, investing in a well-suited coil wrapping machine is akin to laying a solid foundation for a successful business avenue. Reliability intertwined with performance – this philosophy remains at the heart of my decision-making process in every subsequent acquisition.