As I embarked on the challenging yet exciting journey of purchasing a steel coil wrapping machine, my head swirled with questions and possibilities. This investment, vital for streamlining and securing my industrial production, demanded meticulous consideration. I felt the weight of efficiency and reliability resting on my shoulders, yet the promise of enhanced productivity beckoned enticingly.
During my research, I stumbled across a myriad of diverse options, each boasting unique features and advantages. Some machines flaunted cutting-edge technology, while others promised simplicity and affordability. Their diverse uses echoed through industries—from large-scale steel production to smaller, niche manufacturers. My task was to identify which model would seamlessly integrate into my operations while offering significant returns on investment.
As I delved deeper, a clear understanding began to form. It became evident that merely an attractive price tag wouldn't suffice. A more substantial exploration of each machine's specifications, capabilities, and additional features became crucial. Each aspect could become a potential advantage or drawback, dictating the efficiency of my packaging line and, ultimately, impacting my business's bottom line.
Analyzing Key Features of Steel Coil Wrapping Machines
How do you evaluate the operational efficiency of the machine?
The first major element I scrutinized was the machine's operational efficiency. My goal was to find a device that seamlessly integrated into my existing production line while also offering a boost in productivity. This involved looking at wrap speed, automation levels, and machine compatibility. The power source, either hydraulic or electric, was another aspect of paramount importance to ensure consistent operation without downtime.
What are the cost considerations, and how should they influence your decision?
While evaluating the financials, I examined both upfront costs and long-term profitability. The initial purchase price was just one piece of the puzzle. Operating costs, maintenance requirements, and energy consumption all posed as significant variables in determining overall value. For a clearer perspective, here is a simple data representation:
Model | Initial Cost | Monthly Operating Cost | Annual Maintenance Cost |
---|---|---|---|
Model A | $15,000 | $250 | $500 |
Model B | $20,000 | $200 | $600 |
Model C | $18,000 | $230 | $550 |

What is the importance of user-friendliness in these machines?
In my analysis, user-friendliness became a pivotal factor. A machine that was easy to operate not only minimized training time but also reduced potential downtime caused by operator error. Machines equipped with intuitive controls allowed for smoother transitions during operational changes, thus maintaining consistent production flow.
How should one assess the impact of added features?
Beyond basic functionality, I looked at additional features that could significantly enhance the machine's utility. Features such as automatic film cutting, variable wrap tension control, and remote monitoring capabilities could potentially save time and reduce material costs. Below is a structured view of these features:
Feature | Benefit |
---|---|
Automatic Film Cutting | Reduces manual intervention and speeds up the process. |
Variable Wrap Tension Control | Ensures adaptability to different coil sizes and weights. |
Remote Monitoring | Allows for real-time error detection and efficiency tracking. |
For instance, automatic film cutting might increase material wastage.
Exploring Potential Challenges and Solutions
Is machine durability a significant concern?
Assuredly, durability stood out as a major consideration. Investing in machinery that withstands the rigors of daily use without frequent breakdowns was essential. I found that units with robust construction materials and reliable warranty terms significantly eased this concern. Additionally, partnerships with manufacturers offering solid support and easy access to spare parts appeared invaluable.
How should workflow integration and adaptability be managed?
Integrating the machine smoothly into existing workflow and allowing for future adaptability were also crucial aspects. I evaluated how easily the machine could adapt to new coil sizes or different wrapping requirements. Below is a representation of various machines' adaptability features:
Machine | Adaptability Feature | Ease of Integration |
---|---|---|
Machine X | Adjustable Mandrel | High |
Machine Y | Interchangeable Parts | Medium |
Machine Z | Programmable Settings | High |
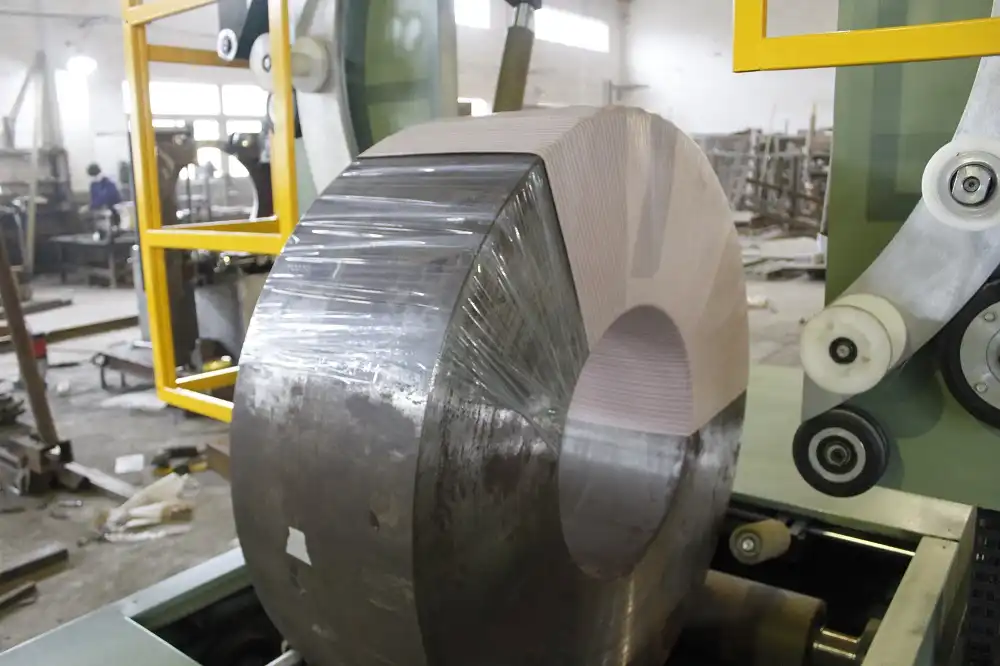
One of the machines, apparently easily programmable, required complex setup processes.
How does one ensure the investment aligns with production goals?
Aligning the purchase with production goals was another layer of the decision-making process. I aimed to ensure that the selected machine not only meets but enhances current production benchmarks. I closely monitored how the anticipated features could impact overall production efficiency and output quality. Long-term visions included scalability to accommodate potential business growth.
Conclusion
Concluding Thoughts on Buying a Steel Coil Wrapping Machine
After navigating through specs and structures, I realized that investing in a steel coil wrapping machine requires a careful balance of technical robustness and cost efficiency. Evaluating each model with an eye toward operational efficiency, cost-effectiveness, and feature functionality became key. Additionally, assuring that the machine fits well within current and future production frameworks paved the path to a sound investment decision.
```